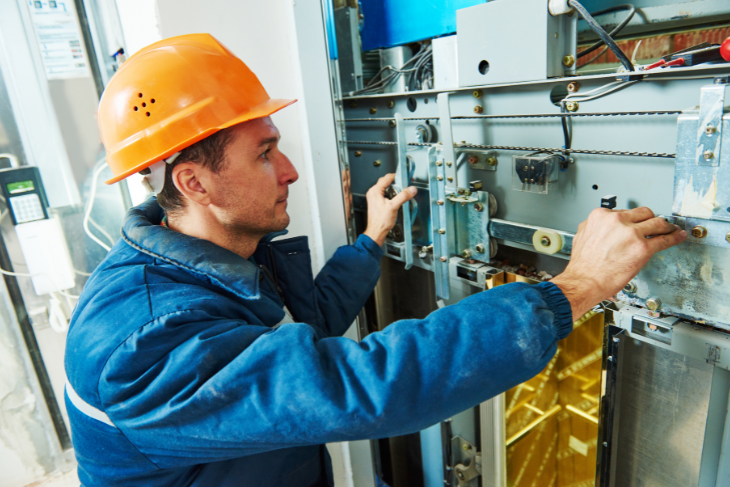
Whether you’re working in automation, CNC machining, or precision manufacturing, PMI linear guides are a key component in ensuring smooth, precise motion. But like any high-performance mechanical system, they require regular care to maintain their efficiency and lifespan. In this post, we’ll walk you through how to properly clean and lubricate PMI linear rails—so your equipment stays running like new.
Why Maintenance Matters
Over time, dust, chips, and contaminants can build up along the rail or inside the bearing block. If ignored, these particles can:
- Increase friction and wear
- Reduce positioning accuracy
- Lead to premature failure of the bearing block or rail
Proper cleaning and lubrication ensures smooth travel, reduces wear, and keeps your machine operating reliably for years.
Want guidance tailored to your application?
Get in touch with our experts today.
Step-by-Step: Cleaning PMI Linear Rails
What You’ll Need:
- Lint-free cloths or industrial wipes
- Mild industrial cleaner (avoid harsh solvents)
- Compressed air (optional)
- Isopropyl alcohol (for deeper cleaning)
Cleaning Instructions:
- Power Down and Secure the Machine
Ensure the equipment is turned off and safe to work on. Disconnect any power and follow proper lockout/tagout procedures if applicable. - Wipe Off Surface Debris
Use a lint-free cloth to wipe off any chips, dust, or grease from the linear rail and carriage. - Use Cleaner or Alcohol for Stubborn Residue
Dampen your cloth with a mild cleaner or isopropyl alcohol and wipe down the rail surface. Avoid spraying directly onto the guide. - Dry with Compressed Air or Clean Cloth
If any moisture remains, dry it using a clean cloth or a gentle blast of compressed air.
Lubricating PMI Linear Guides
Lubrication reduces metal-on-metal contact and prevents corrosion—two major factors in premature linear guide failure.
What You’ll Need:
- Lubricating grease or oil (PMI recommends a lithium-based grease or ISO VG 32–68 oil depending on application)
- Grease gun or manual oiler
- Access to the grease port on the carriage (block)
Cleaning Instructions:
- Locate the Grease Nipple
PMI linear blocks usually have a grease nipple or oil port on the side or end of the carriage. Refer to the model datasheet if unsure. - Apply Grease/Oil Until You See Discharge
Using a grease gun, slowly inject lubricant into the port until a small amount starts to come out of the opposite seals. This ensures full distribution. - Manually Move the Carriage
Slide the block back and forth along the rail to help spread the lubricant evenly across the raceways. - Wipe Away Excess
Clean up any excess grease that may have squeezed out to prevent attracting dust or chips.
How Often Should You Clean & Lubricate?
It depends on usage and environment:
Environment | Maintenance Interval |
Clean room | Every 3-6 months |
General industrial | Every 1-3 months |
Harsh/dusty | Weekly or bi-weekly |
Heavy-duty or 24/7 machines may require daily checks.
Pro Tips for Maximum Lifespan
- Use protective covers or bellows to shield rails from debris
- Always use the correct type of lubricant—wrong oils can degrade seals
- Keep a maintenance log to track service intervals
PMI linear rails are engineered for durability and precision, but even the best hardware needs proper care. With routine cleaning and lubrication, you can dramatically extend the life of your rails and keep your motion systems working like a charm.
PMI linear guides offer the precision, durability, and performance your application demands. Contact us today for pricing, availability, or a custom quote!