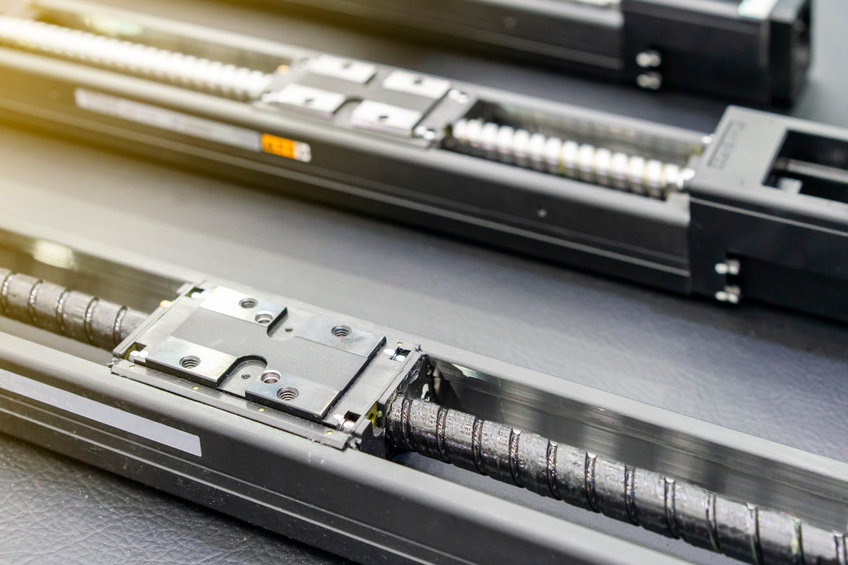
The manufacturing industry is always changing, thanks to new technologies that increase efficiency, precision, and cost savings. One of the key players in this shift? The electric actuator. While pneumatic and hydraulic actuators have been the go-to for years, electric actuators are quickly becoming the preferred choice in many automation setups. They’re playing a huge role in modernizing everything from robotics to assembly lines. Let’s learn more about the basics of electric actuation and how they are changing the game.
The Basics: Electric Actuation in Manufacturing
An actuator takes energy—like electrical power—and turns it into mechanical motion. Electric actuators, specifically, use electric motors to create either linear (straight-line) or rotary (circular) movement. They’re a staple in automated systems because they’re incredibly reliable and versatile. Unlike pneumatic or hydraulic actuators, which rely on compressed air or fluids, electric actuators offer more precise control, are easier to integrate, and are much more energy efficient.
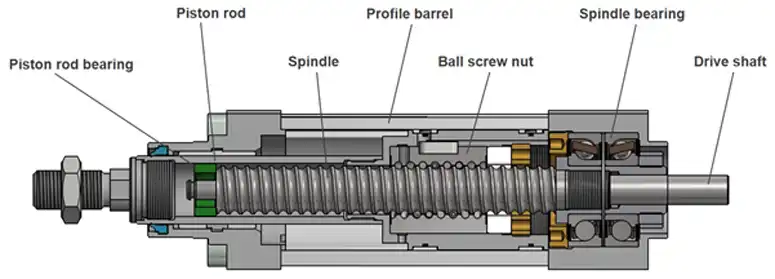
Image courtesy of IMI
In manufacturing, electric actuators are ideal for a variety of tasks—like moving components, controlling machinery, and adjusting positions—helping keep everything running smoothly. You’ll find them in everything from conveyor belts and robotic arms to automated welding machines and CNC machines. Essentially, they’re everywhere automation is at work, making processes more efficient and precise.
Our team of skilled engineers are available if you need sizing assistance or selection tools to quickly size the right product – Actuator Inquiry
Precision and Accuracy: Elevating Manufacturing Standards
In manufacturing, precision is everything. Whether you’re putting together small parts, adjusting machine settings, or positioning robotic arms, accuracy is key to achieving consistent, high-quality results.
That’s where electric actuators shine. With advanced feedback systems like encoders and sensors, they can achieve sub-millimeter accuracy—essential in automated systems where even tiny mistakes can cause defects or waste. Take assembly lines, for example: electric actuators position parts exactly where they need to go, minimizing errors and ensuring quality assurance.
And when you compare them to pneumatic actuators, which can struggle with inconsistent force due to changes in air pressure, electric actuators provide a more reliable, consistent performance. This makes them perfect for delicate or high-precision work in industries like electronics, automotive, and aerospace, where control and repeatability are crucial.
Speed: Driving Faster Production Times
In manufacturing, speed is a competitive advantage. With supply chains more connected than ever and consumer demands on the rise, manufacturers are under pressure to cut cycle times and ramp up production.
That’s where electric actuators come in. Thanks to their fast response times and quick acceleration and deceleration, electric actuators help manufacturers boost production speeds without sacrificing precision. This is especially key in high-speed processes like pick-and-place systems, material handling, and packaging.
Additionally, electric actuators are super flexible. Unlike pneumatic systems that may require tweaking air pressure or valve settings, electric actuators can be easily reprogrammed to fit different production needs. This makes it easy for manufacturers to quickly adjust to changes in production schedules or product types, helping them stay fast and efficient.
Not sure which electric actuator you need for your application? Email us and we can help you through the selection process.
Cost-Efficiency: Reducing Operational and Maintenance Costs
One of the main reasons manufacturers are making the switch to electric actuators is the potential for big savings in both operational and maintenance costs. While the initial investment might be higher than pneumatic or hydraulic systems, the long-term savings can be significant.
- Energy Efficiency: Electric actuators are more energy-efficient than pneumatic or hydraulic systems. Pneumatic systems need a constant supply of compressed air, which gets expensive to generate and maintain. Hydraulic systems come with costly pumps and fluid management. Electric actuators, on the other hand, only use the energy needed for the task at hand, cutting energy costs.
- Lower Maintenance Costs: With fewer moving parts than their pneumatic and hydraulic counterparts, electric actuators experience less wear and tear. No need for regular maintenance of compressors, hoses, or fluid reservoirs. This means less downtime, longer equipment life, and lower repair costs overall.
- Simplified Control: Electric actuators are super easy to integrate with existing control systems, which makes designing your setup simpler and avoids costly infrastructure changes. Modern systems like PLCs and industrial PCs can manage multiple electric actuators at once, making them a great choice for larger automation projects without breaking the bank.
Versatility and Integration: Supporting a Range of Applications
The versatility of electric actuators makes them well-suited for a wide range of applications across different manufacturing sectors. Whether it’s in automotive production, food processing, or electronics assembly, electric actuators can handle a variety of tasks with ease.
In robotics, they’re the driving force behind robotic arms, enabling fast, precise movements for tasks like welding, assembly, and packaging. Because electric actuators can be programmed for specific jobs, manufacturers achieve more flexibility in designing custom robotic systems for their unique needs.
On assembly lines, electric actuators help position and move parts with great accuracy and repeatability. This cuts down on human error, reduces the need for manual intervention, and speeds up production. Plus, since they can handle different loads, one actuator can be used in multiple stages of production, making things even more efficient.
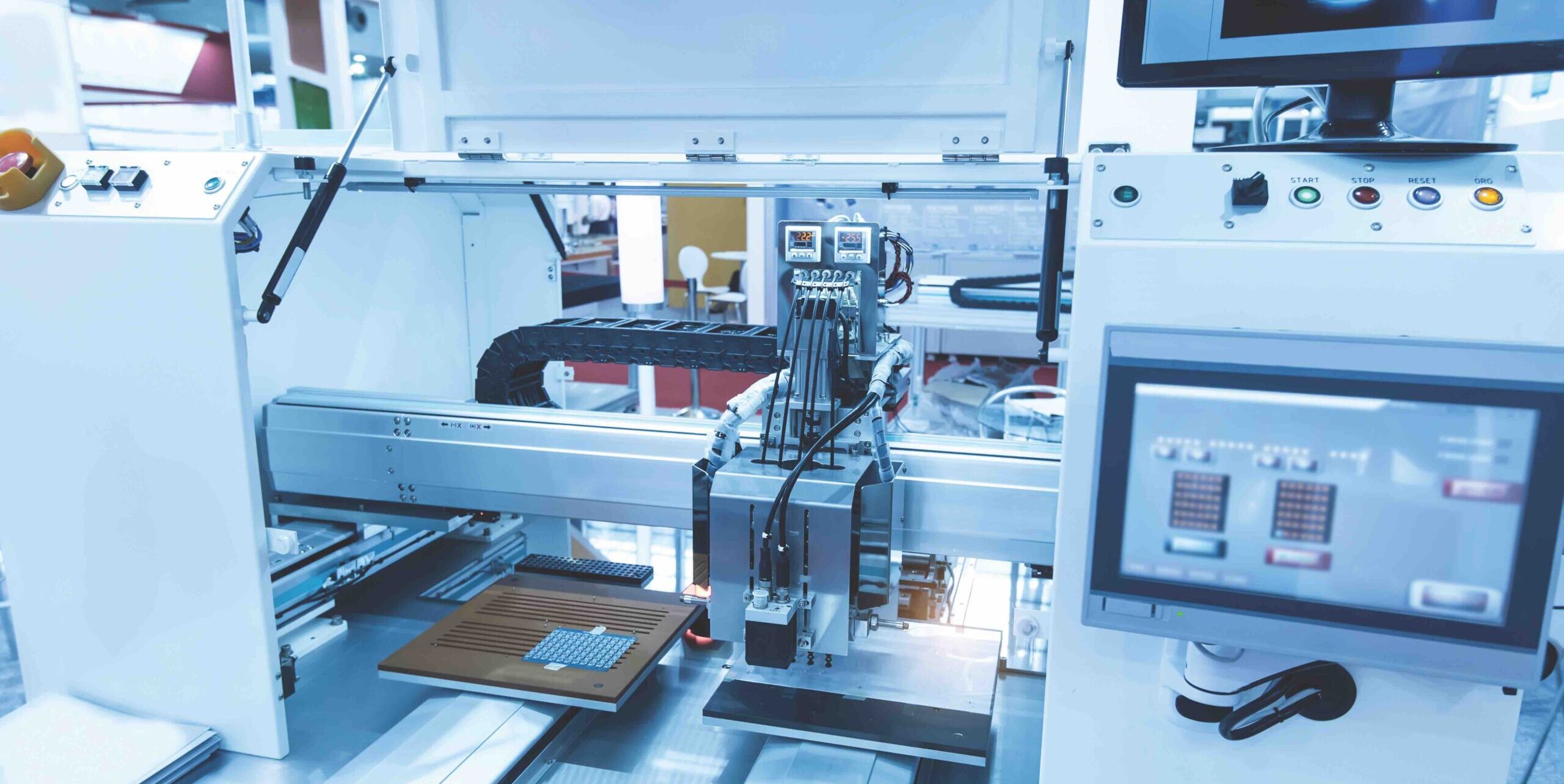
Conclusion
Electric actuators are changing the landscape in manufacturing. By offering precision, speed, energy efficiency, and lower operating costs, they’re turning traditional production lines into lean, flexible, and fully automated systems. As more manufacturers adopt electric actuators, the benefits will continue growing, pushing the next wave of innovation in automation. Whether you’re running a small shop or managing large-scale industrial automation, electric actuators are quickly becoming a must-have in modern manufacturing.
By making the switch to electric actuators, manufacturers can increase efficiency and stay ahead of the competition in a fast-paced market.
Need assistance in the design, selection and implementation of your project? Our team is here to help!